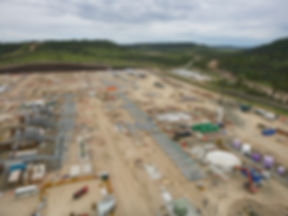
Registered Professional Engineer Queensland (RPEQ)
Chartered Professional Engineer (CPEng)
SIGNIFICANT PROJECTS
These are some of big projects that the team have worked on, such as the AIRBUS A380, the largest project in europe of it's time, GLNG Fairview Hub 4 for Santos ($1.5Bn) and also QCLNG installing two FCS's out of seventen ($1.8Bn)
QCLNG - Field Compressor Station Installations - Andy Nunn
Overview
Site based senior project engineer(2IC) for QCLNG FCS Kate (2IC) & FCS Poppy, approximately 100-120 personnel on each site. For the first 4 months on this project we had no site manager so Andy was "acting site manager". Each FCS installation works valued at approximately $30M installation, out of $1.8Bn over entire project (There were 17-off FCS installations and 4-off Central Processing Plants [CPP]). Overall the entire installation package took approximately 3 years to complete. Each FCS typically comprises 4-off Enerflex supplied (Howden WCVTA 510 screw compressors), requires approximately 2200 dia inches of pipe welding, and around 80T of structural steel erection.
Responsibilities
-
Accountable for cost, resource, forecasting, budget, personnel management. Compiled a forecast estimate between $28-$30M and completed for $28.5M.
-
Signatory for procurement requests up $10K & personnel request approvals
-
Responsible for cost reduction strategies, without impact on quality or schedule deliverables.
-
Performing performance review of staff personnel
-
Accountable for compliance of active construction workpacks for mechanical aspects of site construction including, ITP’s, method statements, FIC’s etc. Management of technical queries. Site installation methodologies & planning, including risk management strategies. Developing methodologies to “work smarter not harder”.
-
Project management including change and risk management of Greenfield coal seam gas project
-
Accountable for schedule, budget and quality performance for site.
-
Compliance with internal and client QA/QC documentation requirements
-
Accountable for the accuracy and approval of “as built” records
-
Accountable for the construction methodology, including management plans and scope of works.
Achievements: Mechanical Completion installation of structural steel, carbon steel pipe and equipment installation delivered 3 weeks ahead of schedule and approximately $2M under budget overall.
FCS Kate & Poppy were the two cheapest install costs of the 17-off that Thiess installed for QGC. Both were delivered ahead of schedule and under budget.
Fuel Farm Installation - RAAF Amberley - Andy Nunn
Overview
The Fuel Farm installation was part of the major upgrade to RAAF Amberley. This was required to facilitate the arrival of the C17 Globemaster into Australia, as the existing fuel farm was incapable of delivering the required fuel flow rates for the C17.
Works included a completely new fuel farm comprising 2-off 1.6 Mega litre fuel tanks, associated pipe-work, pump sets, filtration, motor control centre (MCC), fire supression system, water separation system, full PLC control system with SCADA monitoring front end. There was a change in scope so that the new fuel farm had to interface with existing Fuel Farm. This also meant that I had to review all existing pipework and valves for fitness for purpose and ensure the finished product complied with current standards.
Project value $15M
Repair of the existing Fuel Farm – The existing fuel farm needed upgrading to interface with the new Fuel Farm. Critical area of the plant will be renewed to facilitate interface with the new PLC controller/ SCADA in new Fuel Farm.
Project value $0.5M
Fuel Hydrant pipeline system - In addition to the fuel farm, a dedicated underground hydrant fuel pipeline was required to be installed to supply fuel from the fuel farm via the hydrant fuel pipeline to the runway apron for direct refuelling of the C-17 Globemaster transporter. Works consisted of underground pipe-work network (approx 1.4km). We experienced significant problems with MIC corrosion of the weld due the fact that the entire apron was submerged under water for approximately a week and the the clay soil resulted in high chloride levels, triggering corrosion. After investigation my recommended course of action was significant rework of the affected welds. Approximately 40% of the welds were affected by this. Project value $4.5M
Responsibilities
-
Maintain compliance with management policy
-
Provide expert technical support
-
Achieve safety performance standard of “No Harm”
-
Deliver projects to committed cost and time targets with all client’s needs met
-
Accountability for progress claims and variations
-
Maintain Project program
-
Ensure Quality system maintained
-
Ensure environmental compliance with project and statutory requirements
-
Maintain and manage communication channels within project to avoid miscommunication
-
Establish positive client relationships
-
Ensure effective cost and expenditure management
-
Maintain compliance of risk management of commercial and personnel aspects
Achievements
Introduced and implemented all documentation relating to hazardous area works, including risk management, policies, procedures, site rules, training and induction packages (this type of work had not previously been performed by John Holland at the time).
Reverse Osmosis water feed pipeline & waste water treament plant feasibility - Lytton Refinery - Andy Nunn
Overview
Caltex is one of Brisbane’s highest users of water.
The purpose of this project was to install a pipeline connecting the Brisbane water pipeline to the Caltex supply feed. 4.3 Mega litres of RO water would supplied to Caltex at the conclusion of the project.
Issues
We experienced particular issues with weld corrosion. The material was stainless steel 316 but RO water is particularly corrosive and unless the welds are strictly controlled it is not uncommon to find that surface corrosion around the weld can lead to “eating through” 6mm of Stainless Steel in three months.
Having worked both in NDT and with Lloyds Register of Shipping as assistant surveyor I had experience of this type of issue. I used this and also researched more specific detail regarding the typical issues and solutions. One such solution was pickling the welds sufficiently that surface is stripped of any residue which may lead to “pitting” or “attack”. The pipeline was in the region of 1.4km long, running right through the middle of the “hazardous area” process plant.
Extensive discussions were held to provide the “best solution”. As an exercise purely for cleaning the welds the estimate was $100-$140k.
The pipeline was chemically etched and went into service after I left Worley Parsons in April 2008
Waste Water Treatment Plant
Overview
On this project I was tasked with providing a solution to eliminate the risk of oil getting into the Brisbane River, as there had been two previous discharges due to inclement weather. Sudden rain down pours cause problems due to surging.
There were a four settling ponds used at Caltex (Lytton) and a decommissioned holding dam & weir which were extensively corroded.
My investigations indicated a need for a additional “storage vessel”, to act in effect as “buffer” or “damper”, then providing a slow feed into the existing ponds. The existing flow route was ineffective as it created a “by-pass” in an overflow situation, thus allowing oil to reach Brisbane river without the necessary treatment.
I was given a set of parameter to work to but out of curiosity I requested waste output tests to be conducted for each of the sources feeding into the treatment system. It was interesting to note that some of the plants were discharging significantly more waste product than was advised to myself and more than the intended limits.
My immediate reaction was that each area of plant should resolve their own issues of waste limits and why they were failing to meet the requirements. By doing this I could then design a system around what it should be rather than merely relative to the levels of discharge that were being experienced at that time. This would make the project simpler and a more efficient design.
The Design
My concept was to use vortex technology to separate the oil and water. This was particularly attractive because the flow rate is merely “multiple” ie. If you want double the flow you purchase two units. This was a simple, reliable and cheap solution which at just once pass could provide output water within acceptable tolerances. My concept could be fully automated, so that maintenance would have been minimal.
Proposed one of two storage “vessels” either refurbish the existing “redundant dam & wier and completely rework both the concrete and mechanics to suit the revised design, or merely provide a “water tank” where contaminated water is pumped into it and then discharged through the vortex filtration units.
The benefits
My preferred design also provided benefit to Caltex as it would have relieved one of the separation ponds from it’s current duty. This could then be used when ships need to discharge contaminated water when docked at the Caltex mooring, as there is currently no facility available to visiting vessels.
CLOUGH SEAM GAS - Brian Excell
Overview
Arrow Energy awarded Clough Seam Gas (CSG) the EPCM contract to install an Exterran Compressor Package (Gas driven Caterpillar Engine coupled to a Single Stage Screw Compressor) expanding the Node 2 facility to seven compressors in total providing an extra 10TJ/day to the Arrow Operation.
Brian was employed as the Project Engineer and required to oversee all works carried out by the Subcontractors, this included Civil, Mechanical, Structural, Piping and electrical.
Responsibilities
All regulatory requirements were met, this included but not limited to:
-
Author of the scopes of work for the Civil, Structural and Piping packages.
-
Issuing of the tender packages to the pre-qualified suppliers, evaluation of these resultant tender packages and issuing letters of intent to the successful parties
-
Progress reporting on the pipe work fabrication workshop
-
Witnessing the fabrication to the relevant codes including ANSI B31.3
-
Ensuring the projects scopes were met and achieved per project contract requirements.
-
Engaged safety systems including “Target Zero” and “Take Five” for the entire project duration
-
assistance with QA (ISO.9001-2008 accreditation) reviews at the fabrication workshop including hydrotesting witnessing and NDT inspections to ensure ANSI B31.3 was adhered to.
-
Assisting with site mobilization and construction phase at site resulting in completion of the civil package and process piping installation.
-
Achieving mechanical completion (completion of the ITP’s) and providing assistance with pre-commissioning activities as requested by the client.
ARROW ENERGY, DAANDINE COMPRESSION PLANT - Brian Excell
Overview
Arrow Energy, owning the right to the coal seam gas reserves in the south-western area of Queensland, known as the Surat basin. Delco was engaged to execute the project and to deliver the Daandine processing facility for Arrow under an EPCM contract. Arrow developed a number of Gas/Water Wells initially delivering 34.67 TJ/d to a facility containing six Enerflex compressors through the central gas processing facility (CGPF).
Brian was employed as the Project Engineer and required to oversee all works carried out by the Subcontractors, this included Civil, Mechanical, Structural, Piping and electrical.
Responsibilities
All regulatory requirements were met, this included but not limited to:
-
Review the prepared design packages in respect Arrow’s operational, installation and safety standards
-
Releasing and evaluating tender packages prepared by the in-house Engineering department.
-
Expediting vendor purchased items to site.
-
Assisted with the quality management process to ISO.9001-2008 accreditation.
-
Materials control including purchasing to assist the in-house fabrication workshop.
-
Material shortfall consolidation and re-ordering functions
-
Co-ordinate the release of the site work packs from the fabrication shop via the paint yard including pipe spool tracking registers to ensure installation efficiencies were maintained
-
Providing fabrication work shop support and scheduling updates to the Project Manager.
-
Executed Arrow’s requests for project variations
-
Resolved engineering/design issues on-site
Capital cost of project $24 million dollars (excluding free issued Enerflex Compressors)
Rolls Royce Trent 900 for Airbus A380 - Andy Nunn
Overview
The work covered at Rolls Royce plc was in support of the Assembly and Test Engineering department, looking specifically at the Trent 900 engine transportation for the Airbus A380.
There were a number of issues regarding the Ground Support Equipment (GSE), which I was tasked to resolve.
Validation was a big problem within the department. There were only two transportation stands used by Rolls-Royce plc. The Roll Over Stand was used purely for transportation and the Multi Purpose Stand is used for transportation and designed to allow engine installation and removal on the aircraft pylon.
The Airbus A380 is the world largest passenger aircraft. One aspect that has to be covered on the aircraft is the installation and removal of engines. This is particularly relevant in the scenario where the aircraft encounters an in flight engine failure, perhaps due to a bird strike. The stricken aircraft has to land in order that the engine can be changed. This scenario is known as Remote Site Rescue (RSR). The particular aspect of interest is the installation and removal of an engine when there are no hanger facilities such as overhead cranes etc.
In this situation the engine is installed/ removed manually using the Airbus boot strap operation. Until February 2006 this exercise had not been successfully completed in an RSR scenario. Rolls Royce plc were given the opportunity to demonstrate how Rolls-Royce plc would cover this situation.
I led a team of engineers in the validation of the Multi Purpose Stand (MPS). This was a far bigger exercise, particularly from a commercial stand point, and could only be executed in Hamburg, Germany. My team of engineers came from various countries USA, France and Germany and required precise co-ordination of both resource and equipment. This exercise had to interface with the Airbus programme so that it in no way affected their programme of works. This was my second international exercise. Airbus management were very impressed with the execution of the validation exercise. The exercise itself was to validate the MPS GSE for functionality, the interfacing with the Airbus “boot strap” operation and the procedure/s used to install and remove the power plant. The exercise was so successful that we even identified issues with Airbus procedures. Airbus have also indicated as a result of the validation exercise that they would like to use the Rolls-Royce plc MPS for installing/ removing the Airbus A380 engines as it will save them a minimum of three hours and maximum of six hours per engine change. This was a significant achievement for Rolls-Royce plc.
There was a failure early last year that led to a failure of the “trunnions” when used by Airbus. This was not a catastrophic failure but the trunnion had experienced “plastic deformation”. After an investigation it transpired that the loads being applied using the Airbus “boot strap” process had not been identified correctly. The loads being experienced were significantly higher than Airbus had advised Rolls-Royce plc. The trunnions had to be redesigned by Advanced Ground Systems Engineering (AGSE). I manage the external design interface with AGSE. AGSE design and manufacture both the Roll Over Stand and the Multi Purpose Stand.
Third Party Design House
I managed the development of a third Trent 900 transportation stand with AGSE which combined both the ROS and the MPS, known as the All Purpose Stand (APS). This stand is intended to allow a Trent 900 to be transported in a Boeing 747 Freighter and also designed to allow the engine to be either installed or removed using the Airbus “boot strap” process.
We concluded the preliminary design review and moved to have the first one manufactured. I compiled the programme for this and made provision for the validation.
Summary
Overall this position required that I establish contacts internally, develop relationships with the customer, designers and other external sources. I dealt with negotiation with the customer, co-ordination and project execution both in Derby and internationally. As a leader I established a good reputation and was regarded as a specialist within Rolls-Royce plc for transportation. This is backed up by the fact that they asked me to organise and execute an international trial at the customer’s premises.
Mining - Ravenswood Gold Mine expansion - Andy Nunn and Simon Barron
Ravenswood Gold expansion project. Structural, mechanical and piping scope, consisting of five conveyors, three crushing stations and a ball mill. Project value is circa $25M. Currently 50 personnel on site, scheduled to increase to approximately 100 personnel.
Responsible for the commercial compliance for site works, tracking and identifying non-scope works. Setting up processes and routines to ensure project personnel work in accordance with the schedule to deliver the project in a safe and timely manner, to the client’s satisfaction. Ensuring roadblocks to achieve the required productivity factors are removed to achieve client deadlines.
TEYS Water Works Treatment / Biogas Project - Simon Barron
Overview
Design and Construct of a biogas and water treatment works with Boiler house and gas boiler utilizing Site produced Biogas.
Project value $22M
Simon was employed as the Site manager and required to oversee all works carried out by the Subcontractors, this included Civil, Mechanical, Structural, Piping and electrical.
Responsibilities
All regulatory requirements were met, this included but not limited to:
-
QBSA guide lines and building certification by local authorities for the construction of three buildings, Operators and aeration pump shed, Fire system and treatment pump shed, Boiler house with control room Crib room and toilet.
-
Compliance to ASME Welding codes.
-
All environmental requirements and certification of Biogas Production and storage.
-
All commissioning and start up processes of all the infrastructure.
-
Compliance of all the assets, as well as the compilation of all the Operate and Maintain (O&M) information.
-
MDR compilation & handover documentation compiled in an approved format.

GLNG - K128 - Fairview Hub 4
for Santos - Andy Nunn & Brian Excell
Overview
One of the biggest projects I have worked on was site based senior project engineer for SMP deliverable items on the K128 GLNG Compressor Station No.4, managing 1500t structural steel erection. In addition to this there was 5km of above ground carbon steel pipe & 13km of underground HDPE pipe installation and equipment installation across site (1km x 1km in size), including 10-off Enerflex HCS compressors, 3-off TEG units & 3-off Gas Turbine Alternators.
Project work directly managed approximately $20M, overall project value approximately $1.5Bn.
Responsibilities
-
Compilation of construction work packs for mechanical aspects of site construction including, ITP’s, method statement, FIC’s etc. Management of technical queries. Site installation methodologies & planning, including risk management strategies. Developing methodologies to “work smarter not harder”.
-
Project management including change and risk management of Greenfield coal seam gas project
-
Accountable for schedule, budget and quality performance
-
Responsible for tender preparation, evaluation and award for onsite and offsite SMP packages
-
Compliance with internal and client QA/QC documentation requirements
-
Field engineering and technical query support
-
Accuracy and approval of “as built” records
-
Reviewing and adapting construction methodology, including management plans & scope of works
Achievements: Completed installation of 1500T of structural steel delivered three weeks ahead of schedule and under budget, through adapting schedule according to available materials and resource. Created reporting system for tracking performance progress of SMP activities using XL spreadsheet.
Over 4 million hrs LTI free were recorded on this project and I am very proud to have worked with a great team of like minded engineers who made the journey memorable.
Fairview Hub 4 & Hub 5 are now operational and it is truely an awesome site to see the finished product.

Compressor Facility Installation including refurbishment of Dresser Rand five stage compressor - Andy Nunn
Overview
Refurbishment of a second hand Dresser Rand five stage compressor. Construction of purpose built process building. Assembly and installation of the compressor, drive motor and associated ancillary equipment including all pressure vessel, inter stage and process pipe work. All “Tie in’s” to existing two compressors and associated process pipe work. Project value $15.8M
Responsibilities
-
Responsible for HAZARD studies/ HAZCONS & HAZDEM facilitation within IPL, looking after the quality and effectiveness of how they are executed.
-
The risk management for all project aspects including personnel, site and company aspects.
-
Cost control and Schedule control. Coordination of Procurement activities
-
Plan, organise and manage the engineering activities of the project team including the timely completion of Hazard Studies and statutory approvals
-
Involved in Contract negotiations and awards
-
Accountable for the contract administration for contractor variations management.
-
Commission and validate plant and equipment performance.
-
Closing out contracts after completion of works
Achievements
During the major works associated with the 2011 whole plant shutdown I successfully completed all Tie In works associated with 3rd HHE project which I was the senior project engineer for. After careful rationalization of the shutdown works I managed to gain a $100k saving due to reviewed process performance gains.
I was trained as a HAZOP “champion” and Hazard Study facilitator for inhouse design reviews for existing plant modification and process modification/ design changes. I facilitated numerous design reviews to ensure the right outcome and compliance with all regulatory standards. Reviews conducted included process modifications, hazardous area MCC design reviews at Incitec Pivot (Townsville). In addition I facilitated numerous design reviews at the Incitec Pivot (Geelong) plant in relation to the installation of the new overhead gantry crane and conveyor systems guarding review for fitness for purpose.
Review of the risk register methodology for records associated with HAZARD studies/ HAZCONS & HAZDEMS. Project completed Dec 2012
Nuclear Decommissioning- Trawsfyndd Power Station - Andy Nunn
Overview
Responsible for the decommissioning of the ponds area of the British Nuclear Group Trawsfynydd Power Station. The specific areas concerned were:
Containment structures for the ponds lanes
-
This work involved tender selection, design, installation, methodology, interfacing with other equipment.
-
The radioactive waste removal facility (building construction, process installation)
-
This was a new build facility involving contractor selection, design, tender assessment, contract placement etc
-
Installation of process equipment within the ponds facility
-
Initiated proposal for the installation methodology for plant and equipment, consideration of dose uptake, number of personnel required, risk management etc.
-
Waste removal from ponds north void
-
Methodologies for waste removal. Investigations into what waste is present in void. etc
-
Waste removal reactor vaults
-
Transfer of existing plant and equipment from one reactor to the other. Process verification (conducted in Sweden). Refinement of existing process.
The Export Building
I was directly responsible for the management of the building design by the third party supplier, the erection of the building and the installation of the process within the building. Responsibilities included tender assessments of prospective suppliers, including the selection criteria used to assess tender submissions.
-
Once a supplier was chosen I was responsible for the day to day management of works with the supplier.
-
I ensured that all Health & Safety requirements were met by the supplier, prior to submission to the site H & S signatory for permits to work, isolation certification etc.
-
Responsible as planning supervisor for the compilation of the Health & Safety File.
-
Ensuring that weekly meetings identify problem at the earliest opportunity and maintain the smooth running of the programme.
-
Responsible for maintaining the integrity of the security fence during zone re-classification for the construction phase. Ensuring that at no point is security compromised, as the ponds area is a restricted area due to contamination levels.
-
Ensuring that building fits around the process, rather than fit the process into the building.
-
Ensuring compliance with all current legislation and customer requirements.
-
Ensuring that the engineering change management process is adhered to and that additional costs are minimised.
-
Providing detailed risk management of pre-cursor ground works, including contingency to cover contaminated land issues.
This list is not exhaustive but does provide some insight into some of the responsibilities held.
General
Compilation of near tem work plans and proposals for decommissioing, accountability for KPI’s, management of contractors and project team, cost reporting including CPI’s, SPI’s (earned value management). Risk management of project, including contingencies, resourcing etc. Ensuring H&S compliance, including HAZOP studies. Compliance with regulatory requirements e.g. NII, British Nuclear Group, SI etc. Control of any radioactive waste removed i.e. transportation and storage. Provide presentations to NII to demonstrate strategies for decommissioning including methods, waste routes, contingencies, storage etc. Monthly reporting to General Manager of decommissioing. Promoting working relationships with the customer and project team to ensure clear channels of communication.
This is not an exhaustive list but constitutes the main activities.
All works were performed relative to the Construction Design and Management regulations. Additionally I had to report directly to the Nuclear Installation Inspectorate (NII) to demonstrate compliance with regulations as directed under site licence requirements.
Stargazer Project - Simon Barron
Overview
Stargazer, registration number N140SC, is a modified Lockheed L-1011 TriStar aircraft used by Orbital ATK as a mother shiplaunch pad for Pegasus rockets. As of June 2012, 35 rockets have been launched from it, using the Pegasus-H and Pegasus-XL configurations.
The first Pegasus launch to use Stargazer was conducted on 27 June 1994, and was the maiden flight of the Pegasus-XL. Previous launches used the NASA-operated Boeing NB-52B Balls 8, which was also used for four subsequent launches, as the original Pegasus could not be launched from Stargazer due to clearance issues. A modified version, the Pegasus-H, was introduced to rectify this.
In addition to Pegasus launches, Stargazer was used for captive tests and transportation of the X-34 hypersonic research aircraft; however, drop tests used Balls 8. Orbital Sciences also offer the aircraft for research flights.[1] It is capable of carrying a 23,000 kilograms (51,000 lb) payload to an altitude of 12,800 metres (42,000 ft).
Pegasus launches using Stargazer are usually conducted from Vandenberg Air Force Base. However, launches have also been conducted from the Cape Canaveral Air Force Station, Wallops Flight Facility, and from launch sites outside the United States: Kwajalein Atoll in the Marshall Islands and Gando Airport in Spain.
In 2015, Stargazer was re-painted to reflect Orbital Sciences' merger with Alliant Techsystems
Responsibilities
Senior independent inspector assuring all regulatory compliance in line with FAA and CASA ensuring aircraft was fit for flight prior to release to the client.

E-7A Wedgetail Project - Boeing Australia - Simon Barron
Overview
The E-7A Wedgetail provides Australia with one of the most advanced air battlespace management capabilities in the world.
The E-7A Wedgetail is based on a Boeing 737-700, with the addition of an advanced Multi-Role Electronically Scanned Array (MESA) radar and 10 mission crew consoles, to create one of the most advanced pieces of technology for the Australian Defence Force. All modifications to the 737-700 aircraft were carried out at RAAF Amberly by Boeing Australia.
Based at RAAF Base Williamtown, the six E-7A Wedgetails are capable of communicating with other aircraft and providing air control from the sky. They can cover four million square kilometres during a single 10 hour mission.
The E-7A Wedgetail represents an entirely new capability for the Australian Defence Force, providing an airborne early warning and control (AEW&C) platform that can gather information from a wide variety of sources, analyse it and distribute it to other air and surface assets.
The E-7A Wedgetail can control the tactical battle space, providing direction for fighter aircraft, surface combatants and land based elements, as well as supporting aircraft such as tankers and intelligence platforms.
Based on the 737-700 commercial airliner airframe, the E-7A Wedgetail features advanced multi role electronically scanned radar and 10 state-of-the-art mission crew consoles that are able to track airborne and maritime targets simultaneously.
The E-7A Wedgetail significantly multiplies the effectiveness of our existing Navy, Army and Air Force, and will help Australia maintain a capability edge well into the future.
The E-7A Wedgetail has participated in Exercise Bersama Lima, Exercise Cope North, Exercise Red Flag, Exercise Pitch Black and is currently deployed on Operation OKRA.
Final Operational Capability for the E-7A Wedgetail platform was announced in May 2015.
Responsibilities
Senior independent inspector assuring all regulatory compliance in line with FAA and CASA ensuring aircraft was fit for flight prior to release to the client

Mining - BHP Olympic Dam SCM17 Shutdown and Acid plant failure repairs - Andy Nunn
Asset management specialist for SMP related issues with fixed and mobile plant and equipment, such as conveyors, crushers, wash plants, rotational thickeners, including mobile plant. Shutdown lead for SCM 17 & Acid plant compliance of contractors executed SMP works. Approximately 8 supervisors and multiple contractors managed. Use of SAP for maintenance planning. Responsible for electrical and control contractor management, including FAT & SAT testing documentation and commissioning planning.

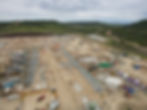

Given all the civils issues we experienced, due to unidentified underground services the finished product is professional
